- 2025 Jan 23
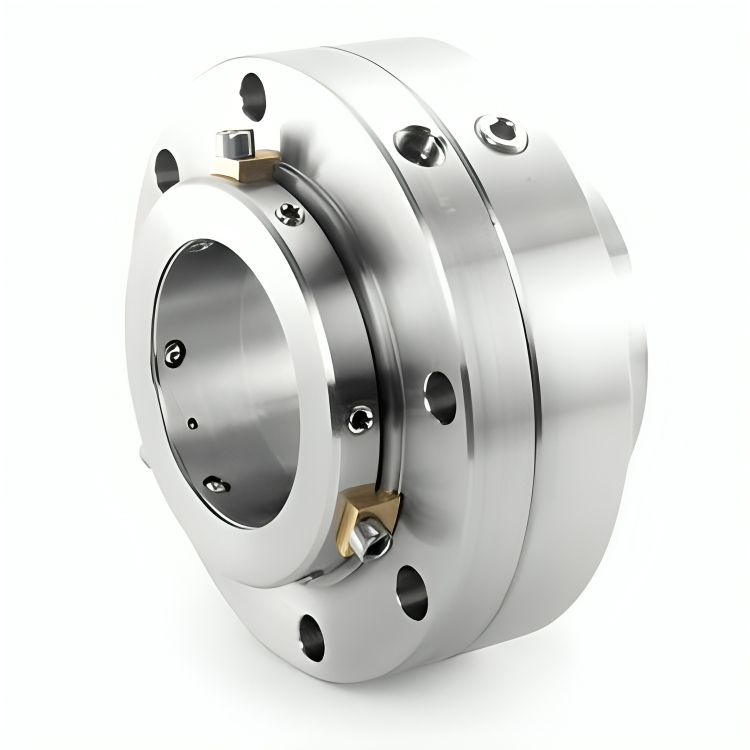
Mechanical seal
Mechanical Seal
A mechanical seal is a component that consists of two flat surfaces, one fixed and the other moving. The main sealing location is the contact surface between the fixed and moving parts, which is perpendicular to the axis of rotation. Usually, the moving ring or ring is the part that rotates with the shaft and is mounted on the shaft by auxiliary sealing rings such as O-rings, V-rings or accordions. This ring is always kept in contact with the opposite fixed surface by spring force. This helps in automatic axial adjustment of the seal according to the movement of the shaft and the degree of wear of the mechanical seal surface.
? How did mechanical flooding occur
The initial idea of mechanical seals was to seal areas where fluid pressure or shaft speed was high. In such cases, simple gaskets and seals are no longer adequate because they must withstand both very high fluid pressure and, on the one hand, engage with a fixed shell, while on the other hand, they must also withstand high shaft rotational speeds. In mechanical seals, the gaskets and auxiliary seals are not exposed to rapid shaft movement and their function is to withstand the pressure of the fluid under seal.
In order for contact between the surfaces to be maintained in the absence of hydraulic pressure, a spring is usually required to apply a load. The applied load must be large enough to maintain contact between the surfaces under various operating conditions. However, if it is too large, it reduces the useful life of the seal. Usually, a coil spring is used in these cases, although, depending on the conditions, an accordion coil spring and elastic rubber components are sometimes also used.
On average, 5 drops per hour or 120 drops per day is the leakage rate of a mechanical seal. The leakage rate in packings compared to mechanical seals is 1080 to 1. Another problem with mechanical seals is the need for high precision in their implementation and construction. Due to the very high surface smoothness, these mechanical seals must be manufactured precisely and, like precision instruments, should be avoided from being placed in a dirty and careless environment.
Advantages of mechanical seals
The best sealing under conditions of high speed, pressure and temperature, especially when minimal leakage is desired, can be achieved by a mechanical seal. The advantages of using mechanical seals include:
► Prevent leakage of expensive, corrosive and hazardous materials
► Reduce maintenance costs
► No leaks that damage the pump or its peripheral equipment.
► No leaks that cause rust and corrosion of bearings.
► No wear on pump equipment due to the presence of sealing components
► No need for an operator, as well as repair and inspection at successive times.
► Reduce the time required to repair or re-seal the pump
Choosing a mechanical seal _ Mechanical seal
Considering that the best choice for sealing is a mechanical seal , the right design must be chosen for this task. There are different types of mechanical seals to choose from, including:
1. Mechanical Rotating Seals:
In this type of mechanical seal, springs or accordions rotate with the shaft.
2. Stationary Mechanical Seals:
In this type of mechanical seal, the springs or accordions do not rotate with the shaft.
3. Metal bellows seals
♦ In some cases, the use of elastomer is associated with problems due to increased fluid temperature, in which case the use of this type of mechanical seal eliminates the existing limitation. This type of seal is most often used in the following cases:
► Non-petroleum fluids
► Seal chamber temperature greater than 400 F (200 C)
► Very low temperatures.
4. Elastomer Seals
They use O-rings or other forms of elastomer.
Used for dangerous or expensive products or any product that needs protection. If your product is any of the following, double seals are used to protect the user.
► Toxic liquid with gas
► A substance that poses a fire hazard
► A pollutant
► A carcinogen
► A radioactive fluid
► An explosive fluid and others
7. Designs that have a fixed interior and use centrifugal force to remove solids from sealing surfaces. 8. Outside seals
Usually, various types of these mechanical seals are made of non-metallic materials for pumps.
9. Mechanical Cartridge Seals
Such mechanical seals make installation easy and allow impeller adjustment without causing problems in the flood surface load.
10. Split seals
This allows mechanical seals to be installed without disassembling the pump.
11. Hydrodynamic seals
Mechanical non-contact seals, which are used to seal gases.
12. Hydrostatic seals
These types of mechanical seals are another type of non-contact vapor seals.
The specific type of sealing job dictates the selection of the appropriate design. If the desired mechanical seal will operate under the following conditions, then there is no serious problem in selecting the mechanical seal material.
► Seal chamber pressures from one ton to 400 psi (28 bar).
► Seal chamber temperatures from minus 40 F to 400 F (-40 c / 200 c).
►The shaft speed in the area should be the speed of the electric motors. If the speed of the seal surface is more than (5000rpm) 25 m/sec, care should be taken in selecting the fixed surface.
►The shaft size should be from 1 inch to 4 inches (100mm to 25mm).
If the seal performance is problematic in the following cases, a special mechanical seal design should be used, including:
► If the seal chamber pressures exceed 28bar - 400psi, then seals that are robust in terms of operation are required.
► In cases where there is excessive shaft movement (e.g. in mixers)
► The mechanical seal must be able to meet the volatile material standards.
► If metallic parts cannot be used in the system, then a non-metallic seal must be used.
► If it cannot be used due to fear of color contamination from black materials, then not just any carbon surface should be used, but two hard surfaces should be used.
► If there is not enough space to install a standard seal, then a special seal must be used.
► Unusual shaft sizes usually require special seals.
Characteristics of a good mechanical seal
Some of the desirable features considered for mechanical seals are as follows:
1. Capable of sealing volatiles without the use of paired mechanical seals.
2. The seal shall not damage the dynamic elastomer or cause abrasive corrosion of the pump shaft.
3. The mechanical seal shall be constructed in a non-compressible condition. For example, the springs shall be outside the fluid.
4. The mechanical seal shall be capable of compensating for appropriate amounts of axial and radial shaft movement.
5. The seal shall be designed to be located as close to the bearing as possible to reduce the effects of shaft deflection. It is best to locate the mechanical seal between the seal housing and the bearing with a large diameter space to provide a large internal radial seal space.
6. The mechanical seal shall generate less heat, heat generated from the seal surface can be a problem for many fluids. Any heat generated between the seal surfaces must be effectively removed from the polished surfaces and the dynamic elastomer.
7. Any dynamic elastomer (such as an O-ring) must be able to bend, rotate, and slide on a clean surface (such as a carbon surface).
8. The load on the mechanical seal surface must be adjustable to balance the effects of impeller adjustment and axial shaft length increases. Cartridge seals do this well.
9. All materials used for sealing shall be of known type and quality.
10. Mechanical seals shall be hydraulically balanced to prevent unwanted heat generation between mating surfaces.
The heat generated during the operation of a mechanical seal can affect the following:
1. Sealing surfaces, especially carbon and coated surfaces or hard coated surfaces
2. Elastomers, especially dynamic elastomers
3. Excessive corrosion of mechanical seal components
4. Heat affects the formed product and causes it to deform.
5. Internal strength of the seal (especially the smoothness of the surfaces and elastomer)